Share this post
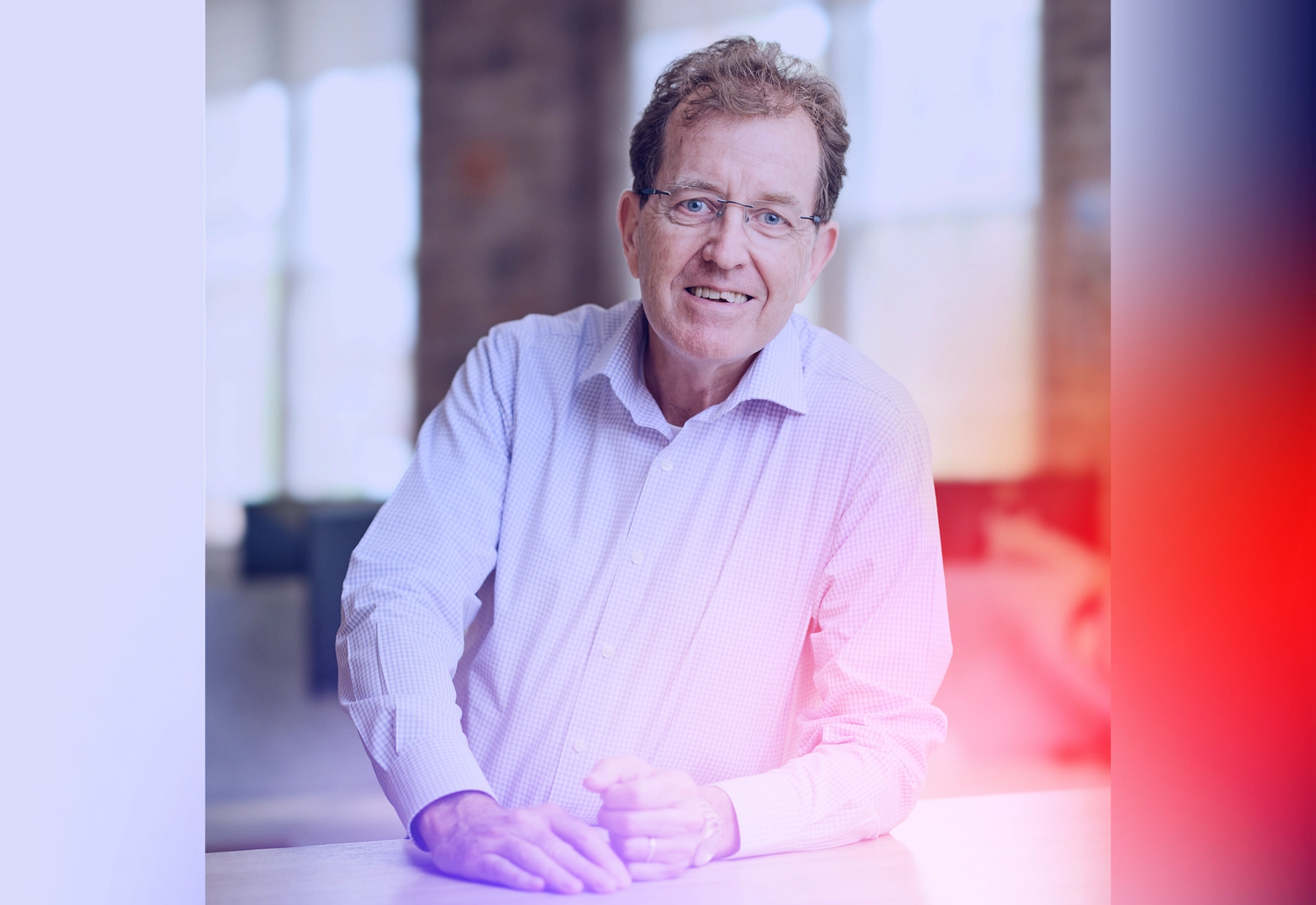
Tell us about yourself and TMX Transform.
For over 40 years, I've dedicated my career to the beverage industry throughout the Asia Pacific region. I've taken on leadership roles in supply chain operations across Australia, the Philippines, Indonesia, and Japan, consistently contributing to the growth and transformation of each location. In 2023, I became part of TMX Transform because of their exceptional ability to provide tangible solutions to supply chain challenges. Whether it involves network strategy, automation design, advanced manufacturing, or digital systems, I have a passion for helping companies shape a more successful future.
What are the key trends and challenges in manufacturing, and what tools and strategies can organizations employ to address them?
On my journey within the manufacturing sector, I've learned that the challenges and trends remain constant, but the approaches to addressing them are continuously evolving. This dynamic presents new opportunities, particularly in fiercely competitive markets.
Take labor costs, for instance. It has consistently been an issue, but with the adoption of automation or globalization (or both), it can transform into a crisis for those slow to embrace these changes.
Similarly, energy costs have always posed challenges. As energy efficiency improves, it presents opportunities for those who embrace this efficiency - but can become a crisis for those who don’t, rendering them less or even no longer competitive.
The same narrative applies to concerns such as carbon footprint and sustainable packaging. Increasing demands from consumers and communities exert additional pressure on manufacturers, sometimes conflicting with cost-efficiency goals.
Labor skill and availability, along with product diversification, complete the list of recurring issues.
For manufacturers, the necessary strategy is to actively stay abreast of technological advancements and other changes that can address even the smallest problems, adopting them as soon as confidence in their effectiveness is established.
Failure to do so exposes businesses to the risk of competitors seizing opportunities, turning minor issues into significant setbacks.
Industries must not passively lament these challenges but should instead take proactive measures. If someone else can produce the same product at a lower cost somewhere else, manufacturers need to reassess their strategies and make necessary adjustments. In a globally competitive market, manufacturers face the pressure to stay competitive by seeking investment and innovation.
To tackle these challenges, industries must actively seek solutions and continuously strive for improvement. Waiting for issues to resolve themselves is not an option; proactive engagement is the key to long-term success in the ever-evolving landscape of manufacturing.
What are the key advantages manufacturers can gain from using automation in distribution centers, and how have these benefits evolved over time?
Warehouse automation offers many key benefits, including manual labor reduction, increased warehouse safety, increased and more consistent output and throughput, and optimized space utilization. Essentially, it enables higher productivity with fewer errors and a reduced workforce.
These advantages become particularly significant when the overall cost of implementing and operating automation is lower compared to manual processes.
Manufacturers stand to gain from all these benefits, especially when warehouse automation facilitates the co-location of storage at or near their manufacturing sites. This not only cuts first-leg transport and offsite storage expenses but also trims down inventory levels.
An important aspect of warehouse automation is its seamless integration with manufacturing automation, allowing for continuous 24/7 operations without incurring excessive labor shift allowances or overtime costs.
The primary takeaway is that the synergy of these benefits results in a substantial win. Lower labor costs achieved through automation, combined with increased output and reduced errors, translate to higher capacity and lower overall costs. While the focus tends to be on cost justification for investments, it's crucial to recognize the added long-term advantages of consistent output quality and improved space utilization. This boosts capacity and allows for higher volume output within the same facility or enhances the output in existing spaces.
In the era of growing e-commerce and heightened demand for rapid shipping, how can distribution center automation assist companies in meeting customer expectations while also staying cost-effective?
A major benefit of automation lies in its ability to rapidly scale up output without the necessity to adjust staffing levels. This implies that, given the right sizing of automation, businesses can effectively meet highly fluctuating demand, especially during periods of tight labor availability. This flexibility extends beyond manual labor tasks, such as picking and moving stock, as automation integrated with order management systems allows for the adaptable handling of administrative tasks like sorting orders to meet demand without the need to adjust the workforce.
Once again, the most difficult part of the matter is capacity. If automation enables the consolidation of inventory into a single location, it presents a significant advantage. Concentrating inventory in one location addresses challenges associated with multiple sites.
Centralizing inventory into fewer locations proves advantageous in the realms of e-commerce and rapid shipping. Concentrating inventory in fewer, or even a single location, facilitates fast delivery and rapid response to market needs, bolstering the ability to manage inventory efficiently.
What are the top factors companies should consider before automating their distribution centers and warehouses?
Achieving a favorable return on investment in automation requires the alignment of key cost and output drivers. Central to this equation are factors such as labor cost, labor availability, property cost, and property availability. Essentially, the higher the labor and property costs, the more compelling the payback from automation.
Additional factors include transport costs, the technical expertise required to manage automation, demand variability, and product type variations. Before opting for automation, companies must thoroughly understand their existing workforce and operations.
A distribution center's (DC) geographical location and associated property costs play a significant role. In areas with low property costs, such as rural areas where real estate is less expensive, the DC type and the likelihood of automation may differ. In contrast to high-rise buildings in commercial or residential zones, rural areas tend to have low-rise structures. The design and implementation of automation are intricately linked to property costs, making high-rise vertical warehousing justifiable only in scenarios where the property costs support such an investment.
A critical factor in automation decisions is the financial payback. For instance, in regions with low property costs, a substantial investment in automation may result in a 10-year payback period.
This timeframe becomes a decisive factor in business decisions, as the financial payback significantly influences the feasibility and success of automation investments. In essence, automation entails a significant upfront investment, requiring careful consideration of financial aspects to make informed business decisions.
Could you provide some real-world examples of successful automation in distribution centers?
Over the past two decades, Coca-Cola in Australia and New Zealand embraced warehouse automation as early adopters, resulting in highly efficient, cost-effective operations. Their capacity to meet peak demand with minimal errors is notably elevated, providing a substantial competitive edge in cost and service. The strategic move of early adoption positioned the business advantageously in terms of cost-effectiveness and service excellence.
During my time in Japan, I spearheaded projects transforming a complex beverage supply chain. This involved integrating large, automated warehouses into four manufacturing sites. This led to the consolidation of smaller warehouses, a reduction in transport costs, and a decrease in inventory levels.
Manual picking processes were replaced with large-scale robotic handling, resulting in overall cost reductions of up to 20%, all while maintaining exceptionally high levels of customer service. This transformation proved to be a win-win scenario for all stakeholders, showcasing the success of warehouse automation in optimizing total costs in the targeted areas.
Warehouse automation has evolved into a substantial industry trend over the years, particularly in the last 5-10 years. It has become a commonplace practice, shaping a major industry in its own right. This widespread adoption has not only provided numerous choices but has also enhanced the advantages associated with automation. The increasing competitiveness of costs further underscores the growing feasibility and appeal of automated solutions in various sectors.
This Q&A was originally published in Manufacturing Tomorrow on March 28, 2024.