Share this post
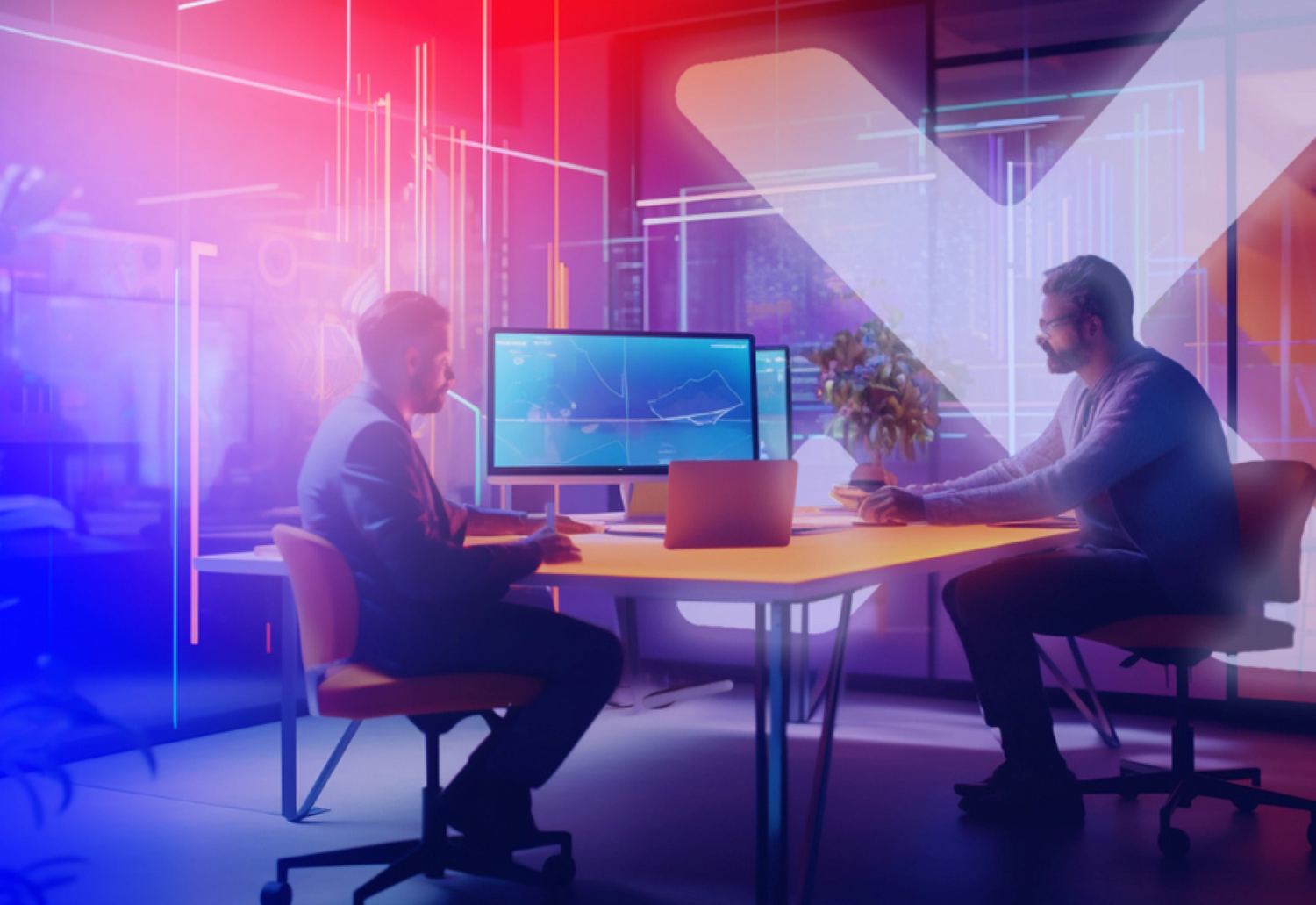
TMX Transform recently polled 250 Supply Chain Decision Makers to discover their awareness and apprehensions around different types of technology. Interestingly, 60% of respondents are unsure about digital twins and simulation technology, and their purpose. Nick De Klerk, our Senior Director of Supply Chain and a leading expert in simulation technology, explores why even seasoned leaders may not fully understand the transformative potential of these tools.
When I read that 60% of supply chain leaders didn’t understand simulation, I wasn’t surprised. The eye-catching figure from the Attitudes to Innovation report highlights the growing gap between the rapid pace of simulation technology development and the awareness in industry. Regardless of its success stories, we must ask ourselves why the practical benefits of simulation remain unknown.
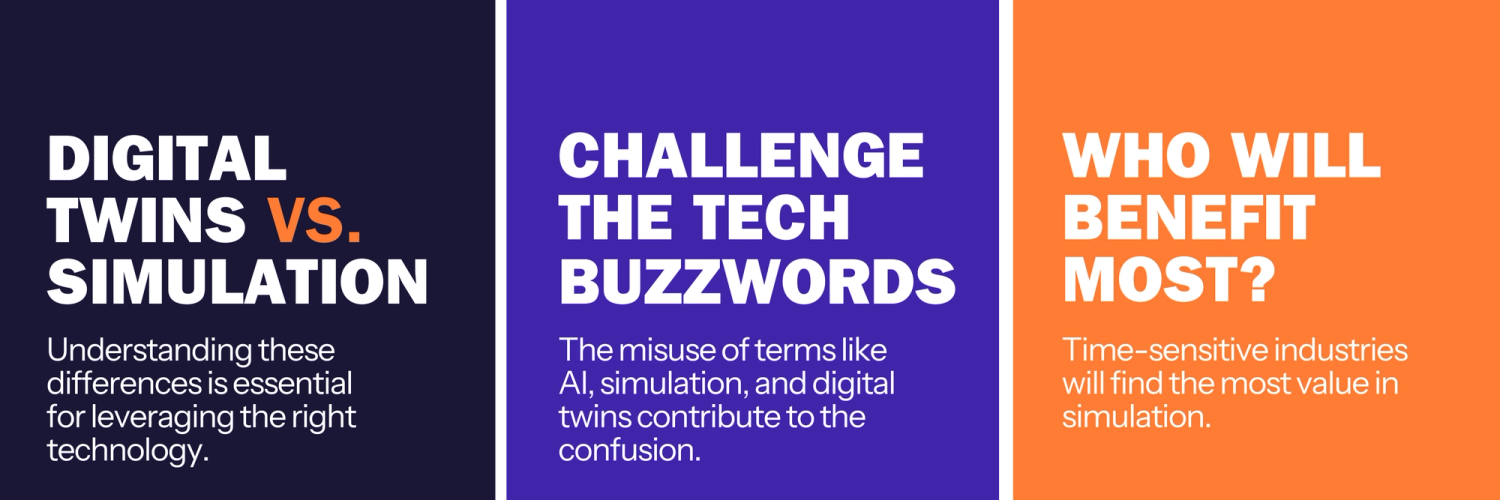
The knowledge gap isn’t helped by the frequent misuse of tech buzzwords in various publications and media. Terms like artificial intelligence, simulation, digital twins, and metaverse are often applied to inappropriate contexts, which obscures the benefits and applications of the technology.
Broad, high-level discussions in media and industry publications often fail to delve into the practical aspects of how these technologies function and, more crucially, how they can benefit businesses. The key questions - "What does it do?" and "How does it help me?" - often remain unanswered, leaving decision-makers in the dark about the real-world applications and advantages of these tools.
Senior Leaders without technical backgrounds may find it challenging to fully appreciate the underlying technology principles, resulting in a less comprehensive understanding of the true potential of these innovations.
This knowledge gap underscores the need for more precise, detailed, and practical information about these technologies in the supply chain context. Here’s a start:
Digital Twins VS Simulation: What’s the difference?
There are three main areas of distinction between simulation and digital twins.
1. Data Connection:
- Simulations use predefined data sets to create digital representations of the physical system for testing scenarios.
- Digital twins operate on a live feed, providing real-time data of the physical system.
2. Focus:
- Simulations answer "what if" questions, allowing users to test different scenarios while keeping other variables constant.
- Digital twins offer a holistic view, focusing on performance monitoring and predictive maintenance.
3. Usage:
- Simulations involve setting parameters, running the model, and analyzing outputs to compare different configurations.
- Digital twins allow for more dynamic interaction with live data.
Simulation is like a flight simulator: A virtual environment where you can test various scenarios without connection to a real aircraft.
A digital twin is akin to a live monitor of an actual flying plane: It displays real-time data on fuel levels, exhaust temperatures, and other critical metrics of an aircraft in flight.
What organizations benefit most from simulation?
Simulation technology particularly excels in industries where time-sensitivity is crucial. Unlike static modelling tools, simulation can effectively assess lead times and the temporal implications of changes, making the technology especially valuable for:
- Fresh food and grocery supply chains
- Postal and parcel delivery services
- Urgent spare parts logistics
The ability to model time-dependent factors gives simulation a significant edge over traditional modelling methods in these sectors.
However, for simulation technology to thrive, an organization needs to adopt specific cultural attributes, including:
1. Self-awareness: Understanding the limits of in-house expertise is crucial. Many businesses overestimate their ability to implement simulation or digital twin technologies independently.
2. Collaborative approach: Successful implementation requires a combination of industry experts who understand the physical systems, and technical experts who can build the digital models.
3. Curiosity: An organization must be open to exploring new ways of improvement rather than being fixed in its current methods.
Despite their potential, both simulation and digital twin implementations are relatively rare in industry, partly because of failed attempts to develop capabilities in-house without the necessary expertise.
For businesses considering simulation technology, it's important to explore the true benefits of the tool and recognize that it may require a blend of internal knowledge and external expertise. Organizations should be prepared to seek outside help to complement their industry-specific knowledge with specialized simulation skills to set up tangible business growth.
If you’d like to learn more about simulation and its benefits, explore our offering here.