Share this post
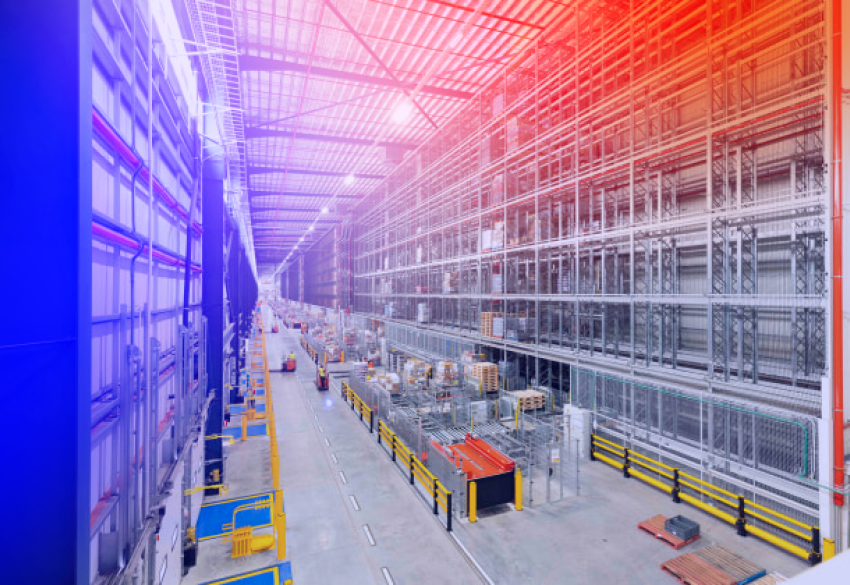
Coles' new, highly automated warehouse in Eastern Australia may be best described as out-sized, starting with the scale of the facility and the automation in it.
The grocery retailer’s greenfield DC, which opened last April in Redbank, Queensland, near Brisbane, is 710,000 square feet (66,000 square meters) in size, featuring a high-bay automated storage and retrieval system (AS/RS) with 65,000 pallet positions that feed into a case-handling, mini-load system with 40 automated palletizing stations.
These systems (Witron) enable the facility to process four million cases a week, the majority as tidy, store-friendly pallets produced without manual case handling.
Matt Swindells, chief operations and sustainability officer for Coles, calls the new “ADC” (A for automated) part of the single biggest investment in Coles’ 110-year history.
And that’s not all. This June, Coles is set to go live with an identical ADC in Kemps Creek, New South Wales, near Sydney. The facilities were designed with the help of an Australian-based global supply chain consultancy and system integrator (TMX Transform), which has recently entered the U.S. market.
Coles went big with automation for multiple reasons, starting with geography. Redbank will service 219 stores, mostly in the massive state of Queensland, roughly 2.5 times the size of Texas, with some distribution to stores in the north of New South Wales.
Together, the two DCs will replace five manual DCs that previously served Queensland and New South Wales, in half the warehouse footprint. But as Swindells points out, the project isn’t just about rationalizing space in the traditional sense. The ADCs will also enable more frequent replenishment, with Redbank already reducing out of stocks by 30%.
It’s all about enabling growth, and enabling growth means you have to hit the right cost base and also the right service level to keep acquiring customers who have higher expectations on both convenience and value.
Part of the cost savings comes from the automation—eliminating the need for teams of workers to manually pick cases or use semi-automated means of depalletizing and palletizing. Streamlined transport route efficiencies to stores and better cubing of trailer space is an added benefit.
Finally, workforce sustainability is a factor, Swindells adds, since in previous ambient DCs, most team members were hefting cases all day. A small number of manual tasks remain at Redbank, but many of the workers are now automation system operators and not materials handlers.
“It’s better for customers, it’s better for shareholders, and it’s better for team members,” says Swindells of the highly automated DCs.
Project drivers
Coles may not be well known to consumers in North America. But in Australia, it’s a major grocery provider to communities across the continent, with online options and a network of retail outlets, which include more than 850 full-line supermarkets.
Founded in 1914 by G.J. Coles as a local variety shop, Coles has grown and evolved to meet customer needs, from advancing the supermarket model in the 1960s to online sales and options for customers.
Today, Coles employs more than 120,000 team members, engages with more than 8,000 suppliers and focuses on sustainability. Coles’ stated mission is, “helping Australians eat and live better every day.”
The retailer’s sustainability focus involves healthy food offerings and sustainable packaging, but it extends to supply chain activities. That’s a challenge when goods need to be distributed across Australia’s geography.
For the eastern region, the twin ADCs will replace five manual DCs, none of which carried all of the ambient SKUs Coles needs to distribute. One of these DCs had been a national DC for ambient goods under an earlier network design, carrying about 12,000 slow-moving SKUs out of the 18,000+ items Coles wanted to distribute. The other DCs carried approximately 6,000 of the faster-moving SKUs each.
Compared to the ADCs, the old network involved longer distances and lead times to distribute SKUs whose order velocities fluctuate weekly with promotions. For example, many of the slow movers had been located at the legacy DC near Sydney, but that required extra lead time to replenish stores in the north of Queensland.
Now Redbank, which can hold 18,500 SKUs, acts as a central efficiency hub for automatically building up optimized pallets of ambient goods and getting them out more frequently to all 219 stores in its region, even with shifts in velocity.
“Redbank brings all the [SKU] range within one state, and it takes one day minimum out of the ambient slow lines to drive a 20% increase in frequency. That’s because now all the slower-moving goods go out at the same speed as the fast-movers,” says Swindells. That represents a strategic shift, since historically national DCs were used to consolidate slow-movers, with aggregation leading to efficiency.
“I think what Covid taught a lot of people is that you can drive that efficiency to a point where resilience is compromised, and your customer offering and your availability can begin to be compromised, and it doesn’t necessarily work,” Swindells explains.
While achieving better stock availability was central to the project, so was workforce safety by automating manual case handling wherever possible. “We wanted to be safer,” says Swindells. “When people are handling 11 tons per day, we were after a material improvement in safety.”
The ADCs reduce labor requirements and cut costs, says Swindells, but the end game is growth.
“I’ve always said that the supply chain exists to enable the business to grow—they aren’t created just to be more efficient. Automation gives us the efficiency, scale and density to be able to put more product closer to our customers,” says Swindells. “So, our network has evolved in part because of the dynamics with the customer, and in part because of what automation enables.”
Project genesis
A major automated greenfield doesn’t go in overnight. Systems this big can take years to plan, install, test and bring up to speed. The time was right to proceed with the projects in 2018.
From the start, the plan was to build both ADCs, beginning with Redbank. At the time, Coles was in the process of assessing the capabilities of the Witron system when several factors fell into place. In addition to the evolving needs of Coles’ customers, leases were expiring on DCs in the existing network. Planning the two projects as one program also had financial advantages.
“We did the proposal for two,” says Swindells. “There are efficiency gains in transport [with two big ADCs], and there are efficiency gains you get in rolling from one go-live to another.”
Coles had used DC automation at some of its other sites before, so it brought in its most experienced automation experts to work on the project leadership, including Diarmuid McArdle, Coles’ head of automation programs, and some experienced system operators.
Other disciplines within Coles also played key roles in the program implementation, including Property, Operations, Transport, Safety, Procurement, Employee Relations and IT.
“You’ve got to put your very best people on it to deliver programs of this scale, and you also must have the wider enterprise behind you,” says Swindells. “Supplier engagement, data compliance [with suppliers], product planning and promotion range—all those aspects need to be worked on in partnership as part of a program like this.”
What the automation does
Redbank is highly automated, though they have a small volume of pick to pallet processes for bulkier items, and a goods-to-person solution for picking smaller health and beauty items to totes. Multiple sub-systems include:
- The high-bay warehouse (HBW) is a pallet handling AS/RS with 65,000 pallet positions and 16 cranes. Before pallets head into the HBW, there are quality control checks on master data and to detect issues like pallet overhang. The AS/RS, which provides automated reserve storage, has two infeed lines on different mezzanine levels to speed up induction.
- Witron’s Order Picking Machinery (OPM) and tray warehouse performs the fully automated case picking and pallet builds. After 16 depalletizers automatically delayer pallets from the high-bay and place cases on conveyor, cases are automatically placed on system trays and enter the OPM- tray warehouse. The OPM has 80 high-speed tray cranes and 40 sequence buffers to stage the cases needed for pallet builds, and convey them in sequence to 40 automated pallet build stations: Witron’s Case Order Machine (COM) functionality. The OPM typically handles more than 70% of shipped case volume per week on a fully automated basis.
- Next to the high-bay AS/RS, a system called the Car Picking System (CPS) supports a pick-to-pallet process for bulky items like toilet paper or dog food that normally make up about 4% of weekly pick volume. Pallet truck operators can stay at ground level to pick, which helps with safety, and replenishment of the CPS is fully automated by the HBW pallet cranes.
- A order picking system, called the All in One (AIO), processes smaller, slower-moving goods like health and beauty items. It includes replenishment inflow, decanting from pallet into totes, a 120,000-tote storage area, 32 pick-to-light workstations and two goods-to-person (GTP) workstations. Also, the AIO area has an order consolidation buffer for picked store totes and automatic stacking, labeling and wrapping.
- To process some of the faster-moving SKUs in the range, Coles uses Witron’s automatic layer picker to pick whole layers of cases onto a single pallet. For example, the store might receive five full layers of soft drinks on a pallet to help with shelf replenishment efficiency in store. Full pallets of very fast movers like soft drinks or toilet paper can also be processed automatically straight from the HBW.
The subsystems are interconnected by conveyor, and multiple quality control and data verification steps are present throughout the operation. It’s enabled by a “teach-in” step, which gathers master data for every new SKU entering the ADC, so the automation knows its dimensions, weight and factors like crushability and stackability.
A key capability of the OPM is that it can build store-ready, aisle-aligned pallets for many order loads, though for the furthest routes, more than 1,100 miles from the ADC, the software is dialed to maximize trailing cubing and transport savings.
We’ve got [automation] kit here that will process four million cases a week, however you want it to be done. The good thing with the Witron system is that we can configure it the way we want. We’ll optimize that over time.
Results and lessons
So how’s it all working? When Modern spoke with Coles, Redbank already had some high-volume operating conditions under its belt, and the system was hitting its marks.
Last December it was processing as many as three million cases a week. “It’s rated for four million, and it’s not even breaking a sweat,” Swindells says. “Everything we did in establishing the design ratings for the system—it’s outperforming already.”
The benefits are shaping up for customers and communities, too. “We’ve already seen availability improvements, particularly for stores in the more remote areas,” he says. “We’ve taken the number of out of stocks on the shelf down by about a third of what they used to be. That’s not a small improvement—it’s a material step change.”
One pleasant surprise is how the new receiving area, pallet conveyor and dual infeeds for the high bay AS/RS have reduced congestion in receiving and sped up truck turnaround time. Swindells says that with manual DCs, the facility typically allotted 90 minutes for truck turnarounds, but at Redbank, trucks are turning around in less than 60 minutes.
Collaborative inventory planning and use of advanced shipping notices (ASNs) with suppliers has also been a long-standing focus for Coles, says Swindells, as has demand planning for its stores. These efforts helped set the right assumptions for the automation project, which is another reason why DC automation projects of this scale need to be enterprise efforts, cutting across disciplines.
“If you don’t have that [collaborative planning] and you are high/low business with high SKU range, you can’t do automation because all you are going to do is automate for noise,” he says. “But when you understand the levers for your supply chain and you can genuinely control them centrally, then you can start to integrate for end-to-end efficiency.”
Looking ahead, Coles is also deploying automation from Ocado Group to create automated micro-fulfillment nodes in key metro areas. Plans call for the new Kemps Creek ADC to replenish ambient goods to one of the first of these sites going up near Sydney.
As Swindells explains, Coles is out to appeal to the consumers on a blend of convenience, availability and value, and the ADCs in its network are part of accomplishing just that.
“From the perspective of supporting our growth for the future, at the right service level, and the right cost, this is a structural shift for us. It’s a game changer.”
This article was originally published by Modern Materials Handling on April 11, 2024.