Share this post
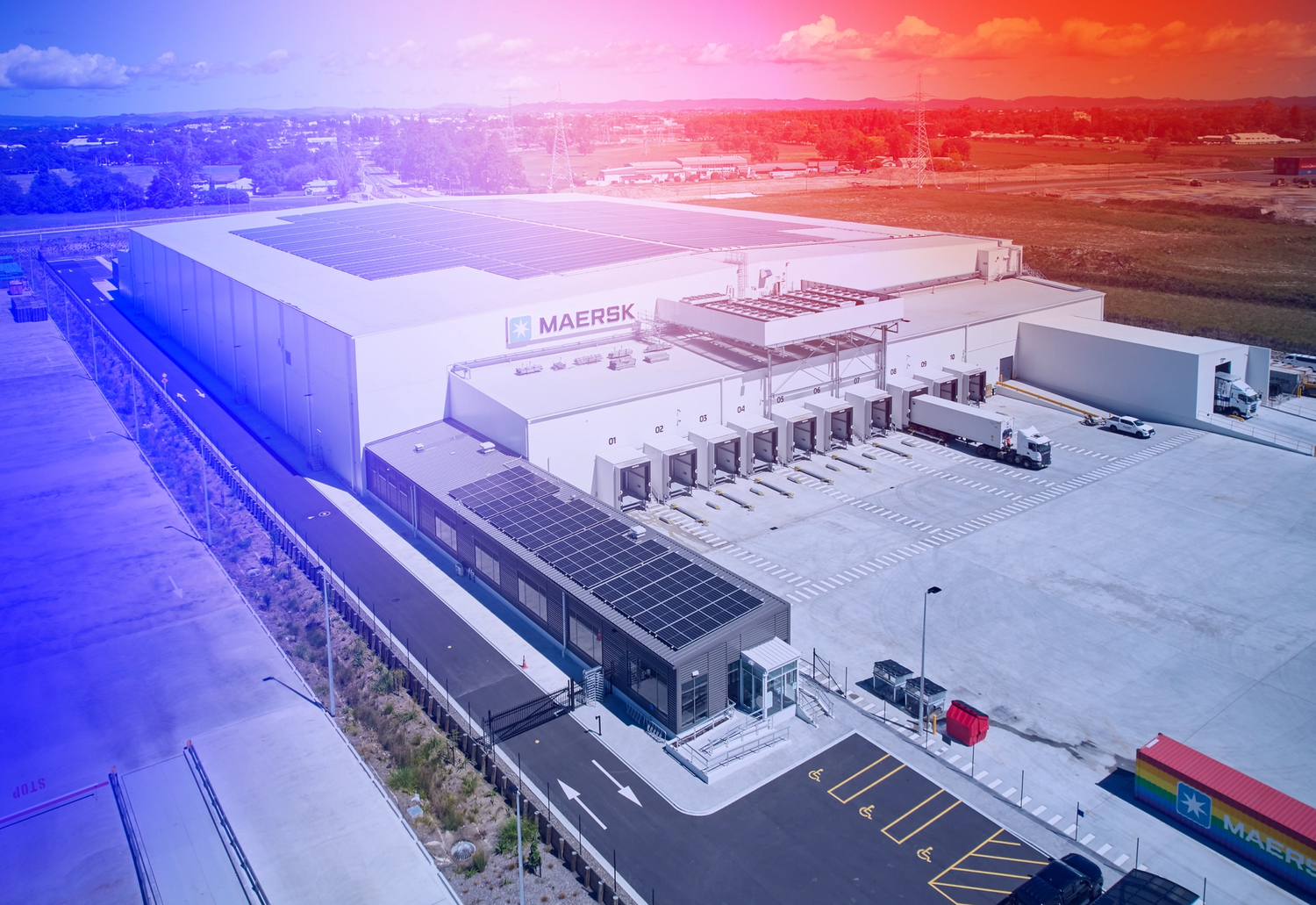
HAMILTON
Taking home the 2024 CBRE Industry Property Award, the Maersk Hamilton Coldstore is a masterclass in sustainable HVAC&R design.
Built to help deliver on Maersk's ambition of being net zero by 2040, its facility in the Ruakura Superhub provides 18,000sqm of coldstore which can house over 21,000 pallets of cold chain products. A fully convertible temperature-controlled space, it can accommodate temperatures ranging from -25°C to 15°C.
Many sustainable practices have been incorporated into the design, with the use and reuse of water onsite as one such example. Condensation is recovered from the defrosting of the evaporators and used to cool the hybrid cooling towers producing enough water to run the whole refrigeration system. Similarly, rainwater is harvested and used for irrigation and the cisterns in the offices.
The site is also fully solar-powered by a massive solar array producing over 1.4MW and the refrigeration system is CO2 (the largest in the world) - using the waste heat for office heating and equipment such as forklifts can be charged in situ allowing for longer operation times and less charging time.
Involved in bringing the coldstore to life, TMX Transform is an end-to-end supply chain consultant, partnering with clients worldwide to transform businesses and optimise supply chains.
Charlotte Arnold, Senior Project Manager at TMX Transform, shares more about the Hamilton project.
What were the must-haves for this coldstore?
Charlotte: From the start, Maersk was adamant that their new coldstore be built in line with their global policy of decarbonising warehouses and coldstores. Maersk also wanted to target a 6-Star Green Star design rating, which is the highest rating a building can achieve in the assessment of its design and construction sustainability outcomes.
Maersk requested the facility use natural refrigerant CO2 rather than the more harmful, but also more common, ammonia. They requested the installation of solar over the entire warehouse, producing more than 1.4MW of electricity at peak production. Electric car chargers and bike facilities are also on site.
It was also crucial to secure an optimum site for the facility.
It is located next to the new SH1 dual carriageway, which is the key transport corridor in the Waikato region and is on a 4.5-hectare site adjacent to the Ruakura Inland Port, making it ideal for the efficient movement of freight between the ports of Auckland and Tauranga.
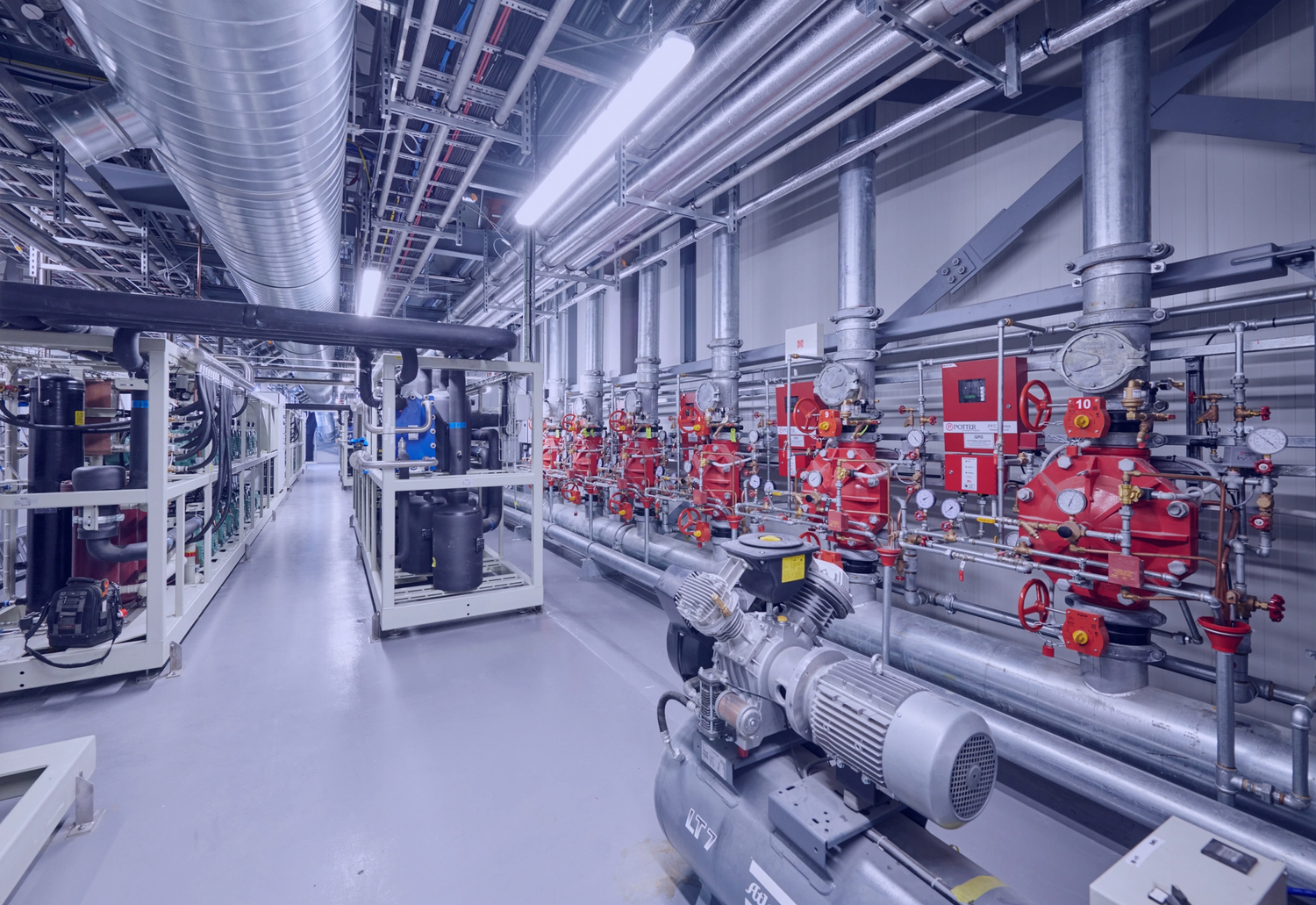
Has this project set a precedent for future Maersk warehouses?
Charlotte: The Hamilton coldstore represents a global achievement for Maersk, of which they should feel proud. Not only does the facility exemplify its global policy on decarbonising global warehouses and coldstoes, but the facility also exceeds the Ruakura Superhub's high environmental standards.
Maersk's ambition is to achieve net zero by 2040 across all their business, and this was top-of-mind during this project, which is a highly energy-efficient facility.
The site has various environmental features and sustainable operations - for example, the building is partly heated from the byproduct of the refrigerant.
What was the process of developing this facility with a CO2 cooling system, without any other refrigerants?
Charlotte: Maersk knew from the start they wanted a transcritical CO2 as the refrigerant. CO2 has a low critical temperature (31°C) and it is a safer and more environmentally friendly alternative to ammonia.
The process for developing cooling systems was integrated into the project's principles and requirements and was led by FGN Consulting in partnership with Apollo Projects, Maersk personnel, Coologic, and TMX staff.
Inputs and guidance from Maersk's own technical cold chain and logistics experts, and the project's cooling consultant Future Green Now, was critical - a true team effort.
For example, during the design process, the layout was modified to transfer the CO2 refrigeration plant from its original remote location to within the facility itself on an upper access way.
A design change reduced 88,000m of piping to just under 7,900m, which greatly reduced the pipe runs to the evaporators, leading to greater efficiency of the refrigeration plant and massively reducing the carbon footprint of the build.
What challenges do you feel are currently involved with constructing and maintaining facilities such as this with HVAC&R?
Charlotte: This project was unique because to mitigate the challenge of additional lead times required for the production and delivery of bespoke equipment, Maersk simply shipped the equipment themselves - improving the efficiency of the overall project.
As well as lead times for custom builds of this scale, a major challenge for any HVAC&R builds is the integration of RMS and BMS systems with client systems. Facilities of this size and scope involve an immense amount of data.
Integrating that data with different systems, including offsite networks which do not necessarily talk to each other, should factor in early in any project of this scale, rather than treated as a later phase.
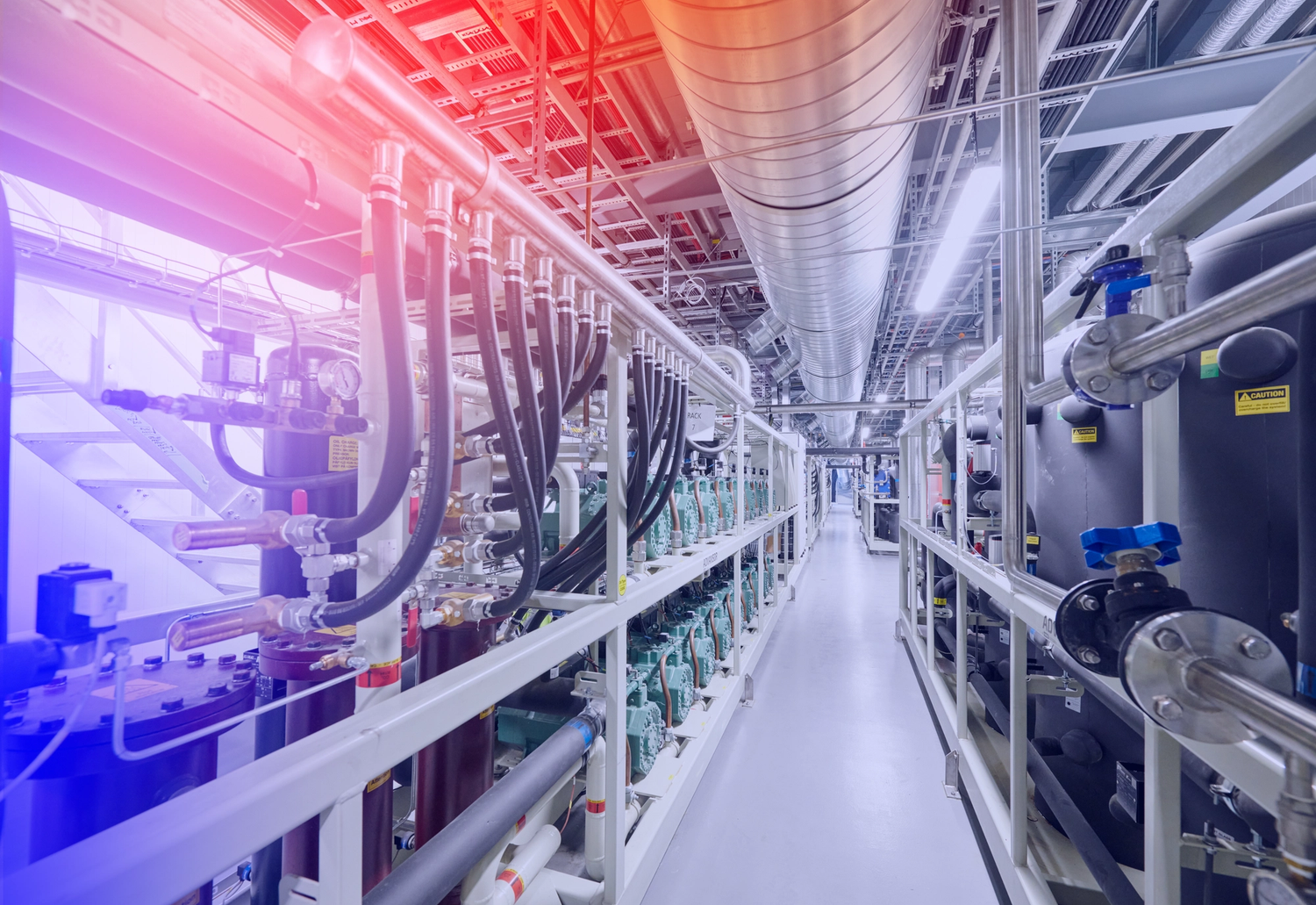
This article was originally published IRHACE Industry Journal's July 2024 edition.