Share this post
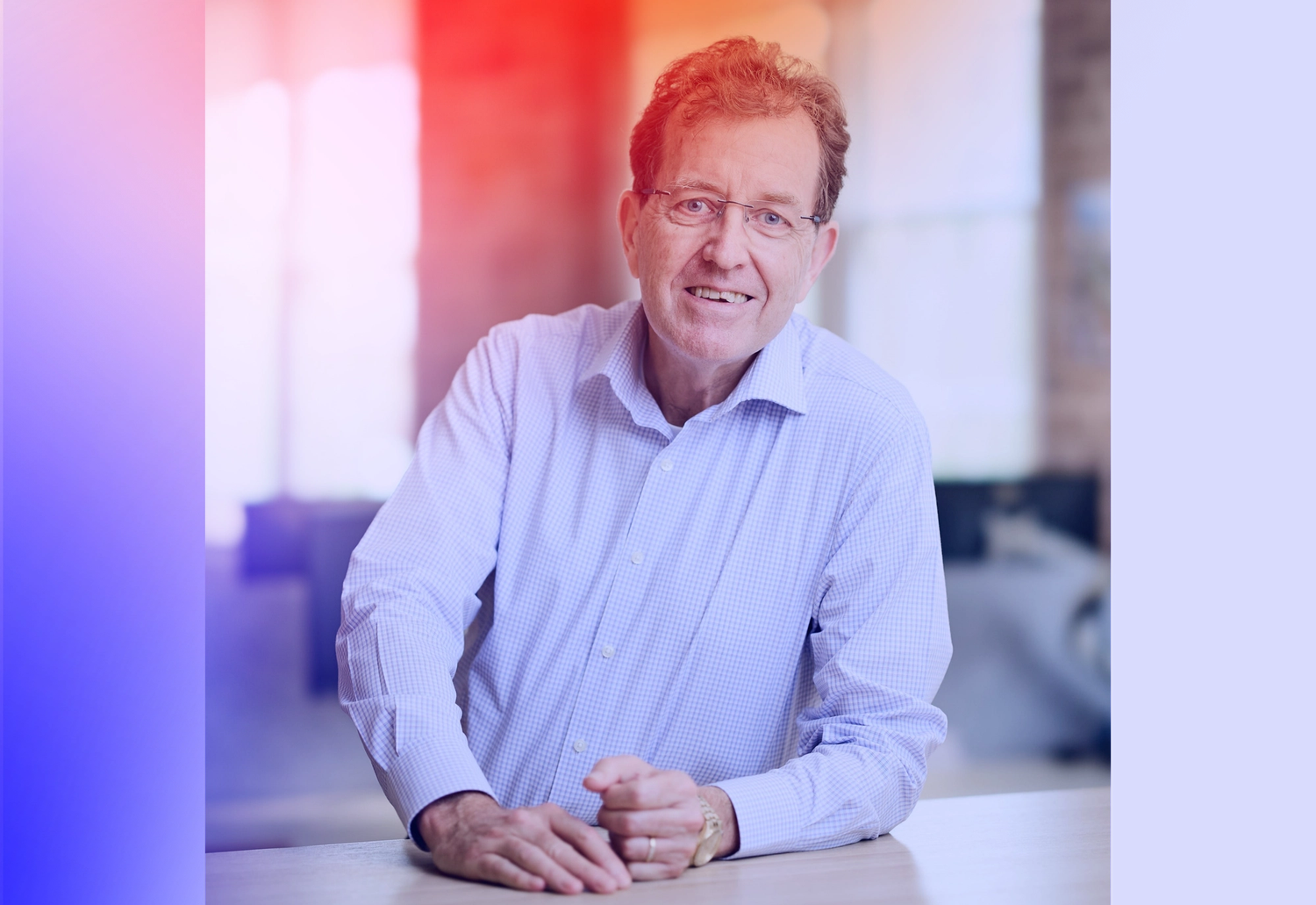
Hybrid work is a hot topic in boardrooms and mainstream media. When this discussion started at scale, four years ago, the case for flexibility for white-collar “knowledge” workers (work largely or entirely performed at a desk with a computer), was made well beyond the pandemic.
The debate now has turned to employer versus employee expectations, scrutiny over productivity, and of course, staff retention and engagement.
But then, as now, blue-collar workers, who perform largely or entirely manual and technical labour roles, are ignored. Blue-collar workers, whether they be in freight, transport, logistics, or warehousing, are the bread and butter of all supply chains. Ignoring them puts your business, and its productivity, at risk.
A workplace should be as competitive as your business
A company's supply chain can become its competitive point of difference if the business directs the right effort and resources towards that objective. Labour is a key part of that discussion.
Last year, Gartner found at least one-third of supply chain organisations lacked an effective employee value proposition. Gartner referred to it as “The Human Deal” – the unchanging trend that in addition to being well-paid, employees want a workplace that is flexible and gives them purpose.
Think about it: you probably want this for yourself too. Businesses with supply chains must invest in their blue-collar workers, from forklift operators to truck drivers to pick packers, and they must provide a workplace that is competitive in the market – or their staff will go elsewhere.
Australia’s unemployment rate is hovering around four per cent, according to the Australian Bureau of Statistics. Finding and maintaining a workforce is a challenge. Engaging them is an even bigger challenge.
A hi-vis vest doesn't mean being seen
White-collar and blue-collar professionals make up supply chains. But in my experience, it is exclusively the white-collar roles who decide for the blue-collar employees, often without consulting the latter.
Further, the HR community and executive attention are more attuned to white-collar and office-based issues than those faced by their shop floor or outdoor workmates.
Office layouts, meeting protocols, and hybrid working are important, but they often get precedence over shift work, public transport, availability of meals outside “office” hours, or working in cold or hot environments.
It is ironic that workers in hi-vis clothing are not always visible to their own leadership. I call this “white-collar privilege”. It’s real. I’ve seen it.
Define your own supply chain status quo
While not in supply chain, a clash of this nature made Australian headlines in 2015, when two painters employed by the engineering unit in Sydney’s Liverpool Hospital appealed to the NSW Industrial Relations Commission, after their employer changed their hours to align with a “whole of hospital” mandate.
The new hours meant the men could not pick up their children from school, whereas the hospital’s administration and nursing staff received this flexibility. Their request was denied.
When staff feel listened to and valued by their employer, they are more likely to stay, and work harder when they do. And as a recent Gartner report points out, supply chain employees are not worried about finding a job. This confidence will last, according to the report, because the ongoing decline in global birth rates will produce a widening imbalance between demand and supply globally.
How will your business prepare for that gap? That same report suggests that while attrition is inevitable in every business, improving your workplace increases the likelihood of good, departing staff potentially returning to future roles.
Start early
Location is the prize in industrial real estate. All parties want to secure the optimum site for a manufacturer, distributor, or supplier. We talk about proximity and access to key nodes – roadways, ports, trainlines, and airports, and the suitability of the site for last mile logistics.
But what about the practical implications for a schedule of round-the-clock personnel working at the facility? When initially scoping a site, a business should always consider its suitability for the future employees. Is there reliable and regular public transport nearby, whether it be buses or trains? If the amenities are not there, local government may need to be approached to discuss adding bus routes.
This is especially key for blue-collar workers in supply chain facilities who work round-the-clock on schedules that do not align with public transport routes, public holidays, or the opening hours of nearby food and beverage outlets.
Visit the factory floor
I was sitting in a boardroom meeting once when an executive announced a new policy that all company property, which includes offices, factories and warehouses, shall be declared a no-smoking zone.
This seemed a reasonable decision. In Australia, since 2006, it has been illegal to smoke cigarettes in enclosed spaces and in outdoor seated areas since 2010. The harmful effects of second-hand smoke are now well known, and most employers find staff smoking in public an unprofessional look for their business.
But no alternative option was offered to shift workers who smoked. I had spent time in our factories and distribution centres enough to know that many of our employees used their breaks to smoke. Declaring all company property a no-smoke zone would force these factory floor workers, sometimes at 2am on a winter morning, to spend ten minutes of their break walking to a poorly lit footpath.
If any of the decision makers in that boardroom were smokers, I doubt it would have required such an inconvenient and potentially unsafe detour from the office for them to take a break.
Why couldn’t we figure out a solution that met the needs of both the company and staff? In that example, the workers ignored the rules, because they felt they had been ignored themselves – and their managers turned a blind eye.
Why your blue-collar workers matter
There is the fundamental human element – that you want to be a good employer and attract and retain good workers. There is also the underlying practicality that if you want your business to survive and grow, productivity matters.
Australia’s labour productivity (GDP per hours worked) indicates economic efficiency, and labour productivity growth has slowed significantly, year-on-year, for decades. It will turn around, but it will take time – and it is not guaranteed for your business. You can start by spending time on the factory floor – talk to your blue-collar workers and listen to what they say. Find out what is most important to them.
Your people are your biggest asset in improving productivity. Make it worth their while to stay at your business. All of them.
This article was written by Bruce Herbert and originally published by Consultancy.com.au on July 1, 2024.