Share this post
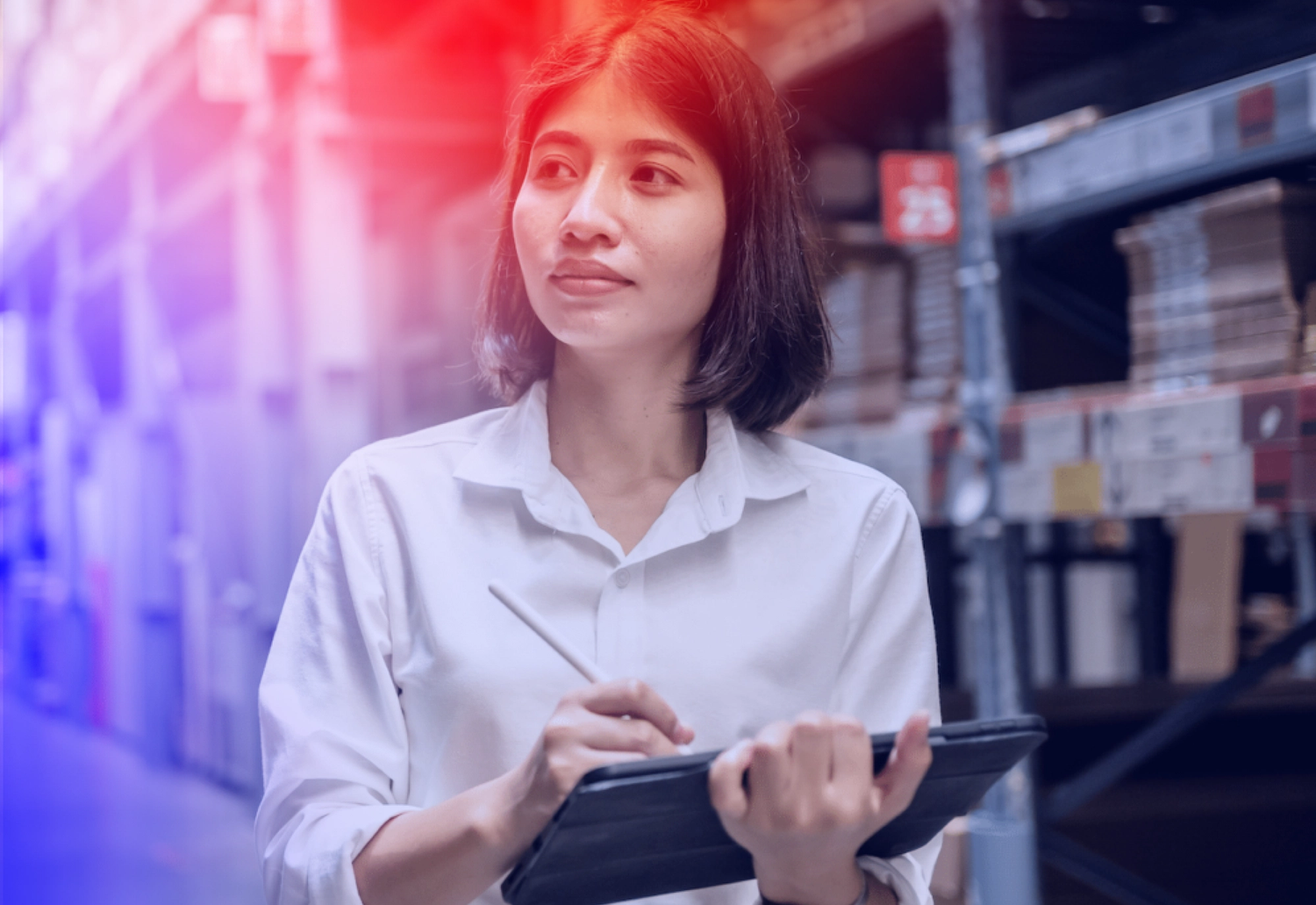
Expect the unimaginable
Despite diligent risk management and contingency planning, I had not even considered the causes of some of the most catastrophic operational disruptions in my supply chain career. Until they happened.
Case in point: on a 13-degree day in April in western Sydney, a hailstorm belted our three-year old distribution centre. The structural impact of the hail itself was not the culprit. The issue stemmed from a subsequent rainstorm, with the hail blocking drainage from the roof, trapping over 200 tonnes of water.
The weight of the water breached the DC roof in two areas, compromising the structural integrity of the building, rendering our key NSW site inoperable, and disrupting the weekly supply of over a million cartons to customers.
A business continuity plan and crisis management process helped the leadership team make quick decisions. Relocating NSW team members and increasing local resources, supplemented our Victorian and Queensland throughput capacity. This increase in capacity, coupled with inventory repositioning and transport reconfiguration, meant customer service resumed within 48 hours. We then secured three local warehousing and distribution facilities to take us through the 16 months until we could return to the original premises.
This ‘black swan’ and other unimaginable events reveal the limitations of relying solely on the assessment of risk. Our risk register did not include the neat line item: “unseasonably severe hailstorm results in trapped water breaching the weight limit of the roof”.
But customers have a right to expect a business to continue to operate.
In an increasingly volatile, uncertain, complex, ambiguous (“VUCA”) world, as we seek resilience in our supply chains, we must also plan from a continuity perspective. Failure to manage business continuity can also impact your team members and retention, your brand value, and your shareholders.
A continuity plan includes alternative methods of operating, should one or more aspects of an operating model fail; a good plan reassesses the feasibility of such scenarios on an ongoing basis. For example, several factors render long-term interstate supply infeasible, so our plan required local alternate warehousing and distribution. Given the hailstorm impacted eleven other companies in our trading estate, the clarity of our plan saw us move quickly and secure alternative facilities.
The new meaning of disruption
Even semantics has been disrupted. ‘Disrupt’ used to mean a game-changing way of shaking up a sector. In supply chain we now see so many con-current disruptions, the industry has adopted the term ‘polycrisis’ (first coined in 1999 by French theorist Edgar Morin).
Supply chains must achieve performance targets despite the impacts of multiple disruptions. Disruptions impact physical operations, such as extreme weather events and labour shortages, and the supply of goods, such as geopolitical conflicts. Supply chains need to contend with shifting demand and contradictory consumer behaviour (in apparel, for example, consumers want fast, free returns but for their vendor to operate sustainably) all whilst contemplating the rising tide of ESG compliance requirements and regulations.
Don’t you forget about me
So why isn’t risk management front of mind for many of us?
Spending time in your business on risk management can be challenging. It is seldom seen as urgent. Risk ownership is often murky. It is clear who has oversight? Who is accountable for the level of risk in a business? The CRO, the Board’s ARC, the CSCO? Has the Board set the company’s risk appetite? And who is responsible for ensuring risk remains in line with the company’s tolerance? Are known risks adequately mitigated and unknown risks contemplated? How are colleagues engaged when mitigations and contingencies require cross-functional collaboration?
Attuning to emerging risk
We tend to think of ‘risk’ in terms of dramatic physical events: a team member injury, warehouse fire, racking collapse, or systems outages. These are potentially catastrophic, but their scale tends to overshadow the far more likely, smaller risk events.
Consumers now interact directly with supply chains, and therefore represent an increasingly significant risk to businesses.
Today’s consumer is more aware of where products come from (think provenance and modern slavery, traceability, and fraud), how product is made, packaged, and shipped (think resource and energy use and associated environmental impacts), and relies on being able to order at the last minute. The link between the sourcing and manufacturing of products, the operational performance of the supply chain, and the company’s brand has never been more apparent.
As business leaders reflect whether their continuity plans are adequate, I’ll leave you with some more examples of the unthinkable occurring during the span of my career:
- At 6am one Sunday, a nearby fuel depot (Google ‘Buncefield depot’) had an explosion that was so large, it devastated nearby buildings and closed the industrial estate. The impact distorted the roller-shutter dock doors and triggered the sprinkler systems, damaging expensive inventory in an FMCG warehouse a mile away.
- A sprinkler pipe burst in the ceiling of a cold storage facility in WA, bringing down the ceiling, ruining the pre-assembled customer orders and turning the freezer into an ice rink. On the second of January, in the middle of a very hot Australian summer, I did not expect to be searching for ice removal equipment!
- A communications cable was accidentally severed in a nearby field, which took the warehouse network offline. Feeling confident of our BCP, to fail-over to the communications provider’s mobile network, we were dismayed to find all telco customers in the area had the same contingency and the mobile service had insufficient bandwidth.
You won’t feel the impacts of the warehouse roof that never collapses, the devastation of a safety incident that never occurs, or the pressure of staff shortages that don’t transpire. But things do and will break, so whilst it is at times comforting that they may not have broken in your business in recent years, the past is not a good predictor of the future.
Businesses need to be confident in their level of resilience. Continuity planning plays a critical role in providing that confidence.
This article was written by Linda Venables and originally published in MHD Supply Chain on March 28, 2024.
Connect with Linda Venables