Share this post

It has been four years since the pandemic began and the world’s supply chains were subject to unprecedented strain and circumstances. But it was not the first time that multiple compounding factors compromised supply chains, and it will not be the last – in fact, there will not be a “last” time. Disruption is guaranteed.
But have companies adapted and built in the resilience needed to future proof their supply chains, to protect their business, and to safeguard their capability in delivering for their customers? Companies still do not know where to start.
With decades of experience between them, senior TMX advisors Linda Venables, Tom Fitz-Walter, and Bruce Herbert share their insights into three aspects of supply chain resilience.

On continuity planning
We are in a volatile, uncertain, complex, and ambiguous (‘VUCA’) world – and you cannot seek resilience in your supply chain without a continuity plan. No matter what happens, customers have a right to expect a business to continue to operate. A continuity plan includes alternative scenarios for operating, should one or more aspects of an operating model fail. A good plan reassesses the feasibility of such scenarios on an ongoing basis. This is where scenario testing, via simulation, can provide such value.
Business leaders can see what the impacts could be to their supply chain and their customers and ensure their plans are well communicated and teams prepared before they materialise. The continuity plan is the blueprint for proactively navigating unforeseen, complex, and disruptive scenarios while protecting customer service.
But while the principles of supply chain resilience are universal, the details are local.
An example from my own career is the time a hailstorm damaged a three-year-old distribution centre in western Sydney, Australia. The structural impact of the hail itself was not the culprit. The issue stemmed from the subsequent rainstorm, with the hail blocking drainage from the roof. It trapped more than two hundred tonnes of water. This rendered the site inoperable and disrupted the weekly supply of more than a million cartons to customers.
Weather can impact a distribution centre anywhere in the world. But the impact, and therefore the required mitigating actions, will differ based on the specifics of the site, its network, the product, and more. All these factors are unique to the timing of the event and the individual supply chain.
In the case of our centre’s damage, we ramped up operations in our distribution centre one state over, while the damaged facility underwent repairs. That solution would not be possible in other parts of the world. Remember, the details are local.
- Linda Venables, Senior Strategic Advisor

On simulation
From the manufacturer to the consumer’s doorstep – an entire end-to-end supply chain – there are countless systemic and physical points of failure or disruption in a supply chain. This is what makes supply chain an interesting and exciting space. It is also what makes supply chains so potentially vulnerable.
Scenario testing, which we do at TMX via simulation technology, is a powerful and effective way to test, and then improve, the resilience of a business’s supply chain.
Because building resilience into the supply chain is not about trying to control what is uncontrollable. It is about strategic planning, supported by facts, which will equip businesses with the knowledge of what to do when something unpredictable happens. We say, ‘what if’ but we should be saying ‘when’, because disruption is inevitable.
Simulation, for example, always starts with a problem. We can demonstrate what happens if your business shifts manufacturing from one location to another, changes the working hours of your labour workforce, tries a new order fulfilment strategy, implements new automation, or test alternatives if primary transport routes become unavailable. The list is endless. Simulation turns abstract or ‘what if’ scenarios into tangible concepts, which means a business’s decision makers can solve a problem before the problem has even occurred.
- Tom Fitz-Walter, Global Executive Director
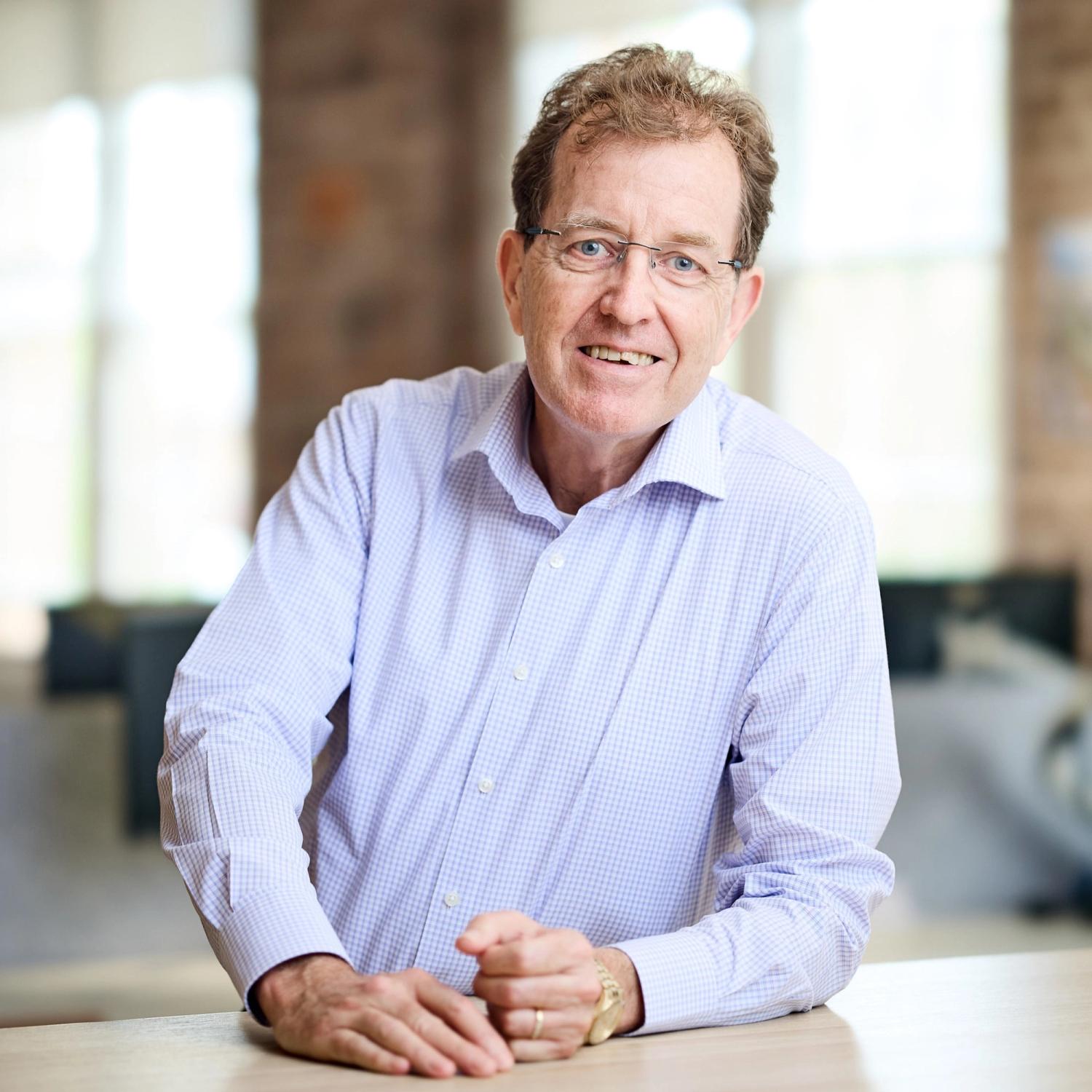
On putting your supply chain to the test
When the pandemic hit, I had been Chief Supply Chain Officer at Coca-Cola Bottlers Japan, based in Tokyo, for more than five years. It was gratifying to see firsthand that the company’s supply chain proved itself extraordinarily resilient – and even successful – through the disruption.
Japan’s experience of serious and regular earthquakes means its population is well versed in crisis management. Add to that a conservative culture, and so our company’s decision makers did not rest in a false sense of security or take risks around supply. This practical, forward-prepared approach meant the supply chain was far less vulnerable than others. For example, there was no single point of failure. Control systems were decentralised and highly manual, and our experienced and decentralised workforces were able to adapt quickly to local disruptions as they happened.
Globally, businesses with supply chains have now experienced their own long-term and wide-reaching supply chain disruptions. None remained untouched.
But the businesses who adopt an initiative-taking approach to resilience will be better off than those who operate in a reactive mode. Multiple businesses are making proactive choices. For example, US-based Garmin, a specialist GPS technology solutions provider, recently announced they will commence production in Southeast Asia in 2026 to diversify their production base.
Globalisation, for all its benefits, has resulted in manufacturers cutting a lot of margins – and therefore resilience – out of their supply chains. For example, the drive to lower costs may mean manufacturing takes place in one large factory rather than across a network. There may be multiple benefits, but there are also risks – and these must be mitigated. Simply being prepared to react is not enough in building effective supply chain resilience.
Risk management is a choice you make now for some time in the future. When that future comes, be sure you made the right decisions when you had the chance.
- Bruce Herbert, Strategic Advisor