Table of Contents
Share this post
Key challenges
Reduced productivity: Increased headcount and overtime costs resulted from congestion in both Inbound and Outbound processing areas.
Suboptimal operational flow: The existing client's facility suffered from operational inefficiencies, impacting overall productivity.
Ineffective workspace: Congestion not only hindered workflow within designated areas but also had a cascading effect on other critical workflows.
Opportunities for OH&S improvement: Identifiable gaps in Occupational Health and Safety protocols prompted the need for strategic interventions to enhance workplace safety.
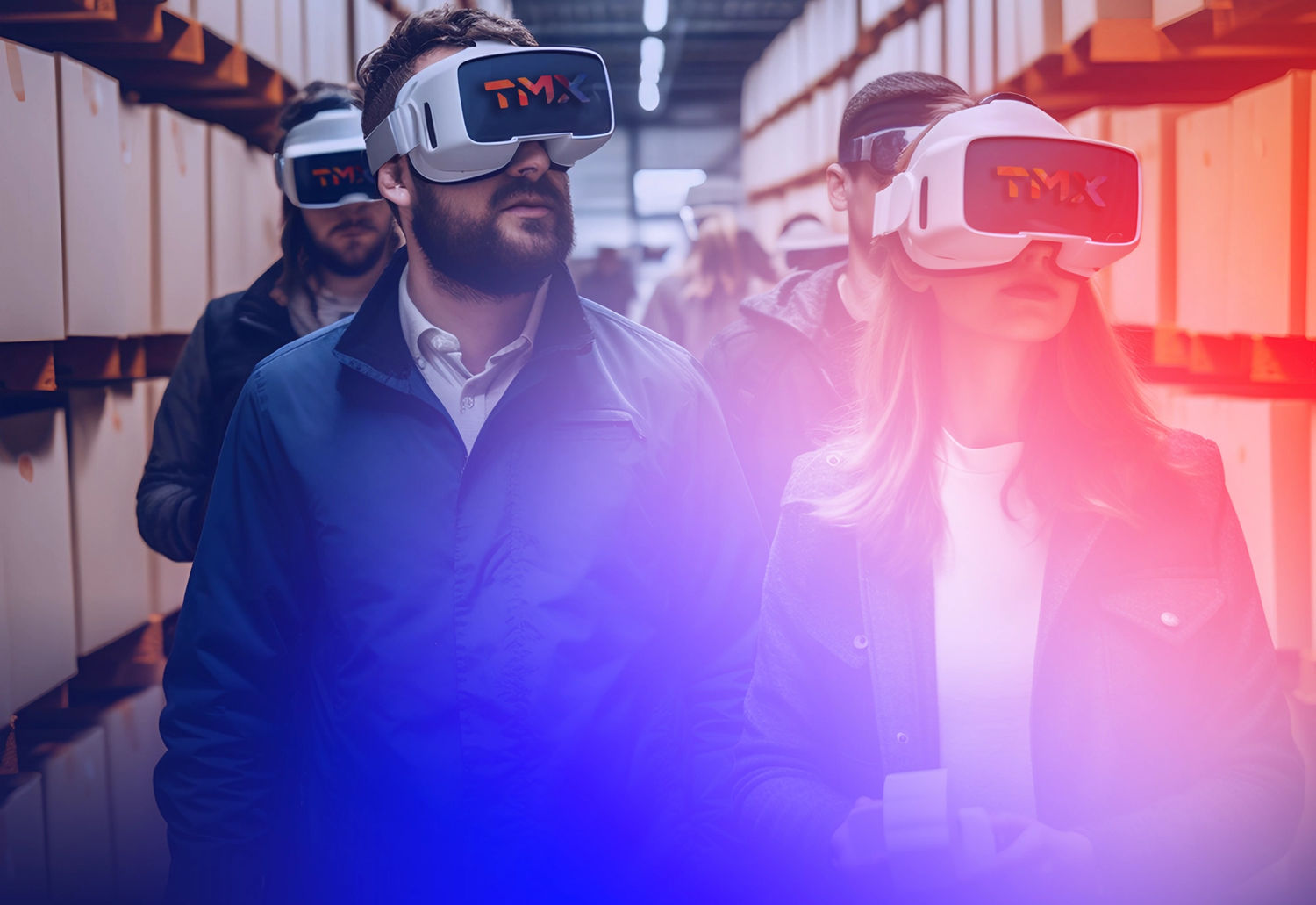
Our approach
TMX was engaged to conduct a comprehensive network strategy review, revealing the need for a new Distribution Center in Melbourne to align with their long-term strategic objectives.
Recognizing the immediate requirement for an interim solution within the existing facility, TMX took a holistic approach to address operational challenges and sustain business continuity over the next 2-3 years.
- Facility assessment: TMX consultants conducted a thorough on-site assessment, gaining insights into existing processes, flows, pain points, and bottlenecks.
- Collaborative design process: In collaboration with the Operations Manager, TMX created a 2D draft layout of the facility. This served as the foundation for the virtual, interactive Meta-clone model.
- Immersive virtual workshop: Leveraging VR headsets, stakeholders from different locations engaged in a borderless virtual workshop within the TMX Metaverse, allowing them to walk through a life-sized virtual representation of the facility.
- Real-time bottleneck identification: Through the virtual model, Project Sponsors experienced firsthand the operation flow bottleneck and constraints.
- Strategic recommendations: TMX's focused on redesigning the processing area to optimize inbound and outbound flow, staging, and reduce congestion.
Additionally, the proposal included quantifying the required heavy lifter units for improved productivity and designing a new Value-Added Services (VAS) area setup to mitigate Occupational Health and Safety (OH&S) risks. This encompassed ergonomic workstations and conveyors to enhance VAS productivity and support future volume growth.
The results
Collaborating in the TMX Metaverse provided real-time visibility of issues, such as daily bottlenecks experienced by Field Operators, allowing the client to share, test, challenge, and validate solutions in real time.
Additional equipment and CapEx were discussed and incorporated during the workshop, enabling the Corporate Sponsor to immediately see the return on the requested investment and its value to the existing facility and performance.
The collaborative decision-making approach, involving stakeholders from multiple levels in a design workshop, played a pivotal role in swiftly finalizing the solution design during a single session, adopting all TMX recommendations.
Various stakeholders and operators actively shaped the final layout, offering valuable insights and sharing historical and operational experiences. This expedited the CapEx design process and demonstrated a commitment to allocating additional funds when needed, showcasing the value of inclusive collaboration in leveraging diverse expertise for efficient decision-making.
Instead of committing AUD$2.5 million for a new facility, TMX provided an interim optimized solution, extending the lifespan of client's existing facility for at least 3 years at a cost of AUD$180,000 (7%). This approach not only offered immediate cost savings but also provided client with a three-year timeframe to strategically plan for their future solution.
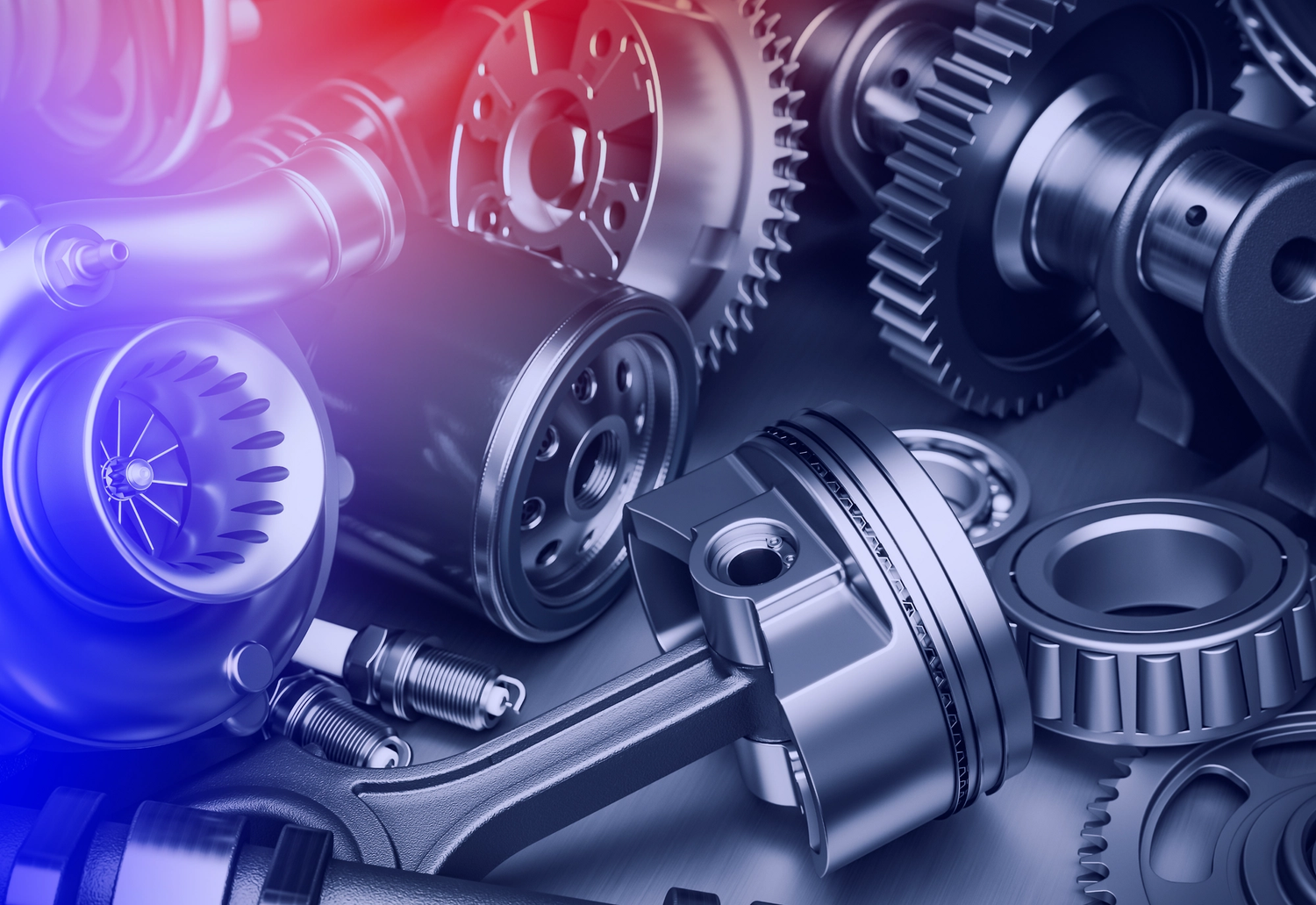