Table of Contents
The world moves fast. Stay ahead.
Subscribe to our newsletter for business transformation news delivered straight to your inbox.
Thank you!You've been successfully subscribed.
Share this post
Key challenges
Teys was facing a number of challenges, across supply chain, property and project management, including:
- Shortage of available purpose-built opportunities within their desired location.
- Design and integration of a food-grade facility that included multiple temperature zones across both a high-bay automated storage and retrieval system (ASRS) and a multi-shuttle system.
- Programming and sequencing of an 18-month automation installation and commissioning period, with lease commencement not until the facility was fully commissioned.
- Port of Brisbane is reclaimed land (sand based), therefore structural piles were required to be embedded 47 meters underground to accommodate the desired Distribution Center (DC) and the slab tolerances needed for the automation solution.
- As a result of Covid-19, mechanical evaporators and structural steel were imported and delayed, requiring re-sequencing of onsite works.
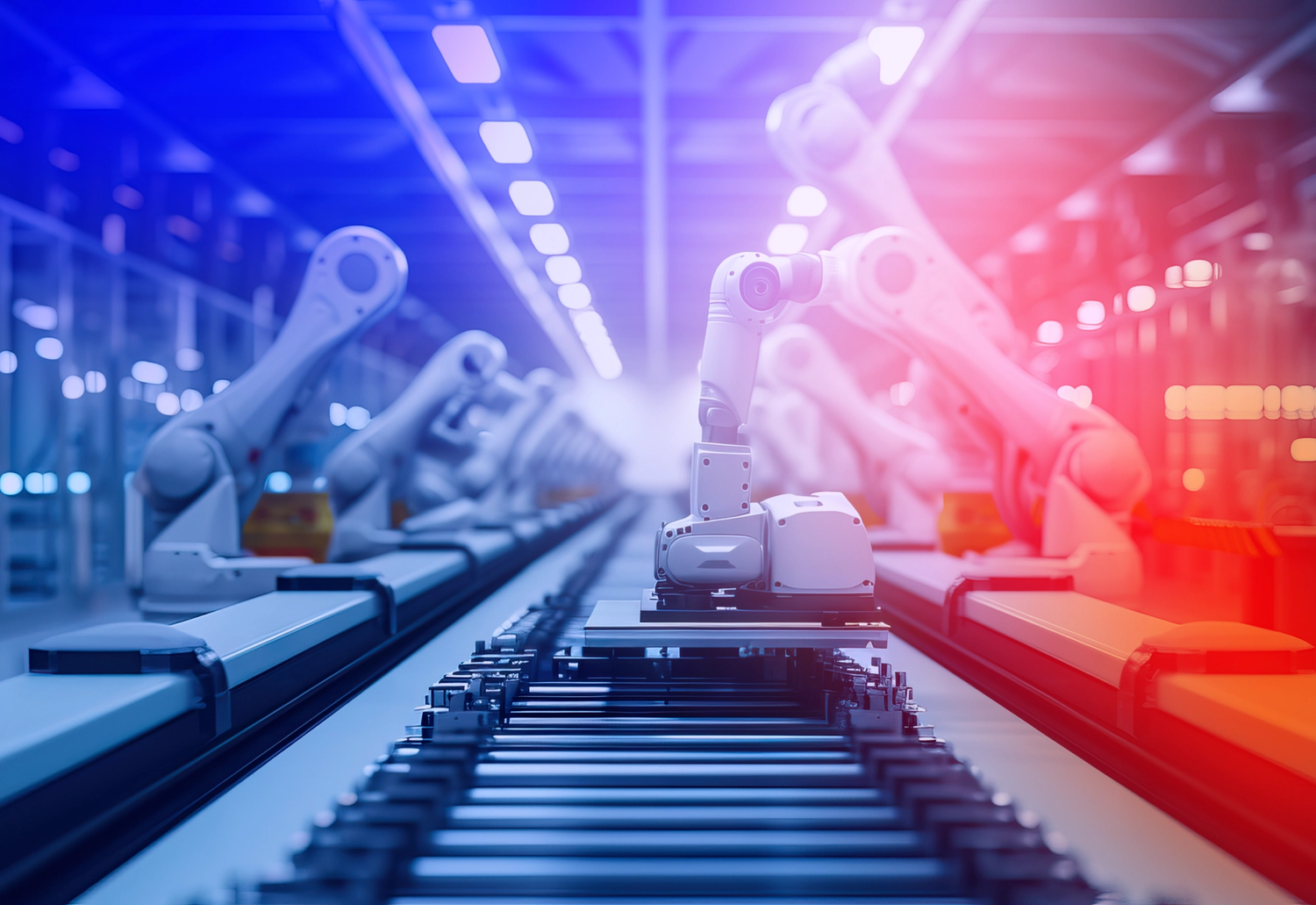
Our approach
TMX undertook:
- Facility and automation design, verifying the property procurement requirement and supporting the business case.
- Property procurement inclusive of landlord funding ~AUD$18.5M worth of tenant-specific building upgrades.
- Preparation of a technical design brief for tendering a purpose-built solution, inclusive of tenant provisional sums solely for Teys’ use.
- Extensive program management of Teys’ business project group working across multiple internal business units (inclusive of comprehensive training). This ensured Teys was prepared for the significant transition to the new processes and systems required for the commissioning of a new DC capable of creating significant operational and logistics cost savings.
Teys required a highly technical facility to accommodate our future business needs, we joined forces with TMX who have provided us with expert advice from start to finish of our project.
— Shaun Johnston, Investment & Innovation Director, Teys
The results
TMX were able to generate significant results through the identified tactical approach, including;
- Five-star Green Star certification achieved.
- Automation solution delivered and integrated into the building.
- 1MW solar system and associated upgrade of building structure resulting in 100% utilization of roof space for solar and minimal distribution of generated electricity to the grid.
- Delays due to Covid-19 overcome due to resequencing of works ensuring the project remained on track for Go-Live.
- Delivered an automated high bay, on the most unstable reclaimed ground conditions (sand) enabling Teys to achieve significant indirect operational benefits, including reduced freight/transportation costs.
- Significantly reduced the successful owners rent review structure, net effective rental rate and bank guarantee during the property procurement process. To complement above AUD$1.3M in additional savings recovered from the successful tenderer during the tender phase for tenant specific building upgrades.
- Design and scope changes were incorporated within the contractual provisional sum allowances, minimizing the cost exposure for Teys.
The world moves fast. Stay ahead.
Subscribe to our newsletter for business transformation news delivered straight to your inbox.
Thank you!You've been successfully subscribed.